As buildings age, their facades can deteriorate and require maintenance. Traditional facade inspections involve visual inspections and manual testing, which can be time-consuming and costly. However, with advances in technology, 3D modelling has become a popular tool for facade inspections. In this article, we will explore the benefits of using 3D models for facade inspection.
What are the main benefits of using 3d models?
The main benefits of using 3d models for facade inspections are accurate visualisation, efficient inspections, cost savings and improved safety.
Accurate Visualisation
One of the main benefits of using 3D models for facade inspection is the ability to create accurate visualisations of the building facade. 3D models can provide a detailed and comprehensive view of the facade, allowing for a more precise inspection of its condition. This is particularly useful for complex facades where traditional visual inspections can be challenging.
Efficient Inspections
3D models can streamline the inspection process by allowing inspectors to view and analyse the facade remotely. This can save time and reduce the need for physical inspections. With the use of specialised software, 3D models can also help identify defects and potential maintenance issues quickly, enabling early intervention preserving facades and preveningt more significant problems from arising.
Cost Savings
The use of 3D models for facade inspections can lead to cost savings for building owners. By providing a detailed view of the facade, 3D models can help identify problems earlier, reducing the need for costly repairs down the line. They can also help optimise maintenance schedules by identifying areas that require attention and prioritising them based on urgency and severity.
Improved Safety
The use of 3D models for facade inspections can improve safety for workers by reducing the need for physical inspections. Traditional inspections can require workers to climb scaffolding or use other equipment to access hard-to-reach areas, putting them at risk of falls and other accidents. 3D models can provide a comprehensive view of the facade without the need for workers to be physically present, reducing the risk of accidents and injuries.
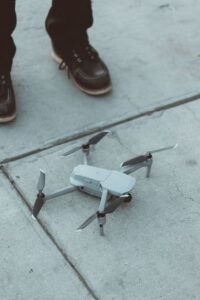
Combining 3D Models with Image Collection Technology
The use of 3D models for facade inspection can be combined with other image collection technologies, such as drones and other sensors. This combination can provide an even more detailed and comprehensive view of the building facade, allowing for more accurate and efficient inspections. For example:
- Drones can capture high-resolution images of the facade, which can be used to create 3D models.
- Sensors can collect data on the facade’s temperature, moisture levels, and other factors, which can be integrated into 3D models to provide a more comprehensive view of its condition.
- Thermal imaging cameras can be used to detect insulation defects, which can be identified and analysed using 3D models.
The combination of 3D models with image collection technologies can provide building owners with a more detailed and comprehensive view of their facades, allowing for more accurate and efficient inspections. This can lead to cost savings and improved safety for workers.
What We’ve Learnt
In conclusion, using 3D models for facade inspection has many benefits, including accurate visualisation, efficient inspections, cost savings, and improved safety. By combining 3D models with other image collection technologies such as drones and sensors, building owners can obtain an even more detailed and comprehensive view of their facades. As technology continues to evolve, the use of 3D models for facade inspection is likely to become even more prevalent, helping to improve building maintenance and safety.
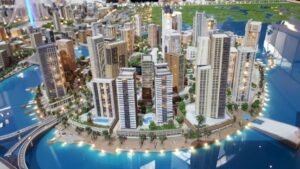